การผลิตอุปกรณ์ประปาแบบแยกส่วนวิธีการแก้ปัญหาในอุตสาหกรรม
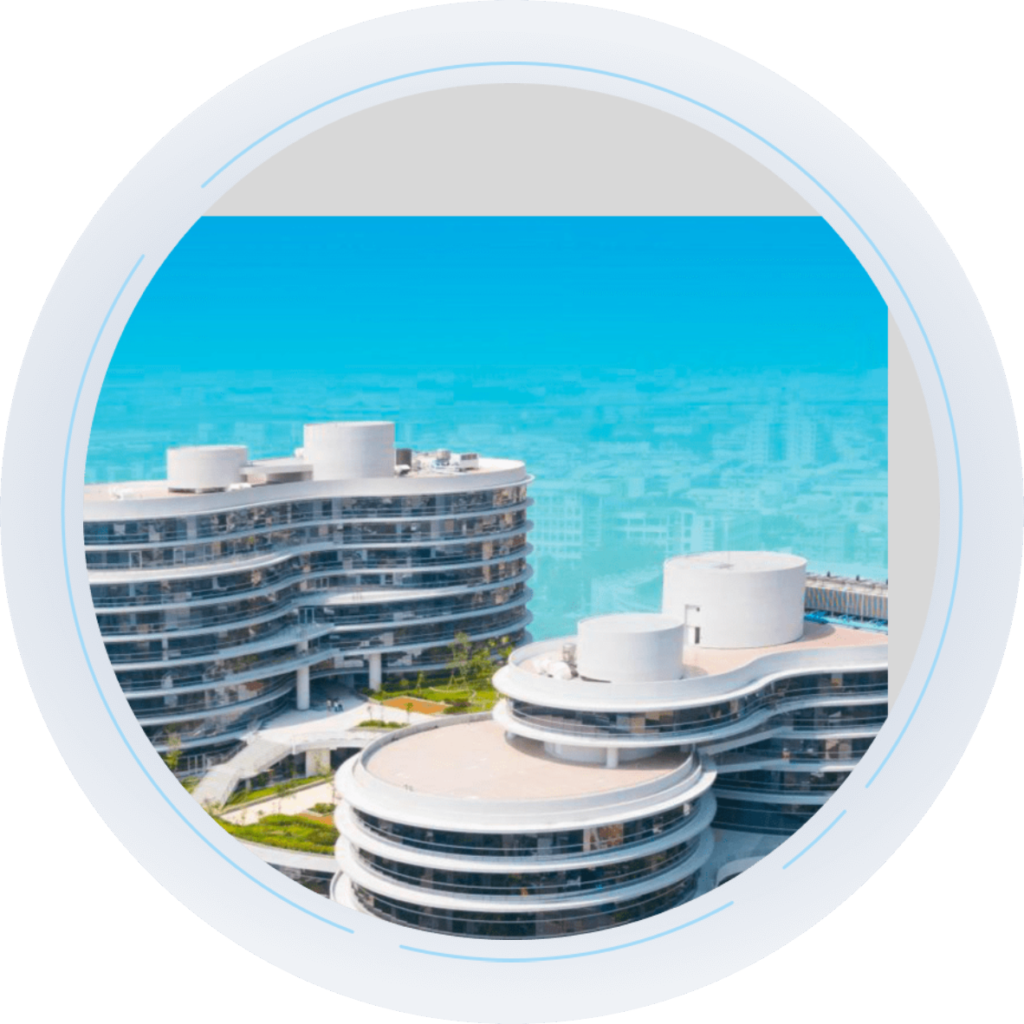
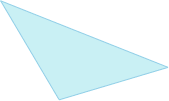
อุตสาหกรรม ความท้าทายในการบริหารจัดการ
การประมาณการและคาดการณ์วัตถุดิบ (ผลิตภัณฑ์หล่อ/ขึ้นรูป) ทำด้วยตนเองโดยอิงจากประสบการณ์ การประมาณการมากเกินไปจะทำให้ต้นทุนสินค้าคงคลังเพิ่มขึ้น การประมาณการน้อยเกินไป หากรับคำสั่งซื้อแล้วไม่มีวัตถุดิบในการผลิต ระยะเวลาการส่งมอบจะยาวนานขึ้นอย่างมาก
การจัดลำดับคำสั่งซื้อ นอกเหนือจากการพิจารณาว่าวัตถุดิบในมือเพียงพอต่อการจัดสรรหรือไม่ ยังต้องสามารถเข้าใจข้อมูลวัสดุ/งานระหว่างผลิต/กำลังการผลิตได้ทันที เพื่อให้ทราบว่าผลผลิตตรงตามกำหนดเวลาหรือไม่
กระบวนการผลิตที่ซับซ้อน มีการกำหนดเวลาเผื่อไว้มาก เมื่อหักลบเวลาที่สูญเสียไปกับความล่าช้าแล้ว อัตราการใช้เวลาทำงานจริงต่ำมาก วงจรการผลิตจึงยากที่จะลดลง
ความคืบหน้าการผลิตเบื้องต้น ไม่สามารถทำตามแผนได้ ปัญหาการจัดเตรียมวัสดุสำหรับการประกอบและบรรจุภัณฑ์จึงยากที่จะควบคุม
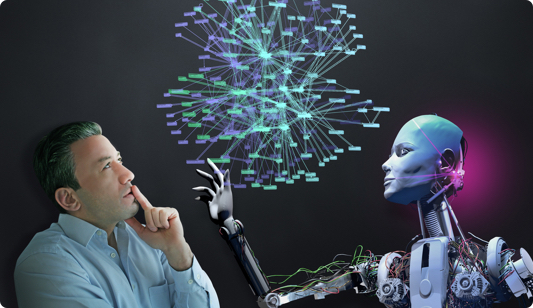
ความร่วมมือระหว่างผู้ผลิตหล่อและซัพพลายเออร์เป็นเรื่องปกติ กระบวนการผลิตหลักแบ่งออกเป็นส่วนการหล่อภายในโรงงาน และการตัดเฉือน CNC การอบชุบ และการเคลือบผิวภายนอก ซึ่งขาดระบบดิจิทัล และดำเนินการด้วยตนเอง ทำให้ยากต่อการควบคุมพลังสนับสนุนข้ามสายงาน ความคืบหน้าการผลิต (เช่น ลำดับงาน จำนวน กำหนดเวลา…) ข้อมูลคุณภาพ… ฯลฯ อัตราการส่งมอบของซัพพลายเชนอยู่ที่ 70% เท่านั้น (ต่ำกว่าอัตราการส่งมอบ 100% ในอุตสาหกรรมยานยนต์มาก)
กระบวนการผลิตอัจฉริยะของอุตสาหกรรมดั้งเดิม 3k ยังคงช้า ส่วนใหญ่ใช้การทำงานด้วยกระดาษด้วยตนเอง ซึ่งเป็น “ส่วนท้าย” ของการผลิตอัจฉริยะ ข้อมูลทั้งหมดไม่ทันเวลา ไม่ถูกต้อง และมีความสมบูรณ์ไม่ดี ทำให้ยากต่อการตอบสนองต่อการเปลี่ยนแปลงมากมายที่เกิดขึ้นในกระบวนการผลิตอย่างรวดเร็ว และยังไม่สามารถตอบสนองความต้องการการผลิตที่ยืดหยุ่นจำนวนน้อยและหลากหลายได้
คุณภาพและอัตราผลผลิตเป็นตัวชี้วัดที่ผู้ผลิตให้ความสำคัญมาโดยตลอด คุณภาพของผลิตภัณฑ์หล่อสามารถตรวจสอบได้ที่สถานีปลายทางของกระบวนการผลิต หรือหลังจากกระบวนการผลิตไประยะหนึ่งเท่านั้น เกณฑ์แรงงานยากที่จะสอดคล้องกัน อัตราการตรวจจับเฉลี่ย 75% ทำให้การควบคุมคุณภาพเป็นเรื่องยาก และความแม่นยำและอัตราผลผลิตยากที่จะทะลุทะลวง ทำให้ไม่สามารถเข้าสู่ตลาดคุณภาพสูงได้
อุตสาหกรรมโซลูชัน
ความรู้
การจัดการความต้องการ การประเมินกำลังการผลิต เวลารอบการผลิต
กลไก
จังหวะการผลิต กลไกการติดตามวัสดุ กลไกการจัดลำดับงาน กลไกการติดตามความคืบหน้าการผลิต กลไกการควบคุมอุปกรณ์
กระบวนการ
กระบวนการยกเลิกการคาดการณ์ความต้องการ กระบวนการกำหนดเวลามาตรฐาน กระบวนการผลิตและการจัดส่ง กระบวนการรายงานความคืบหน้าการผลิต กระบวนการติดตามความคืบหน้าการผลิต กระบวนการเปลี่ยนแปลงสถานะเครื่องจักร กระบวนการจัดการความผิดปกติของการรวมเครื่องจักร
เครื่องมือ
งานบำรุงรักษาการยกเลิก MDS ตารางการติดตามวัสดุ การวางแผนการตั้งค่าพื้นฐาน sMES เวลามาตรฐานผลิตภัณฑ์ รอบเวลาทรัพยากรการผลิต การจัดส่ง sMES การวางแผนการรายงานความคืบหน้า sMES สถานะเครื่องจักร sMES และการวางแผนการใช้งาน
ตัวชี้วัด
จำนวนชุดคำสั่งผลิต อัตราการเริ่มต้นงานตรงเวลาของคำสั่งผลิต วันที่ส่งมอบตามแผนของคำสั่งซื้อ จำนวนวันส่งมอบการผลิต อัตราความสำเร็จในการจัดส่ง
การตรวจสอบ
การเตือนการสั่งซื้อล่าช้า การเตือนการขาดแคลนวัสดุของคำสั่งซื้อ/คำสั่งผลิต จำนวนวันล่าช้าของคำสั่งซื้อ การเตือนภาระคอขวดภายในโรงงาน ตารางความสำเร็จแผนการจัดส่ง
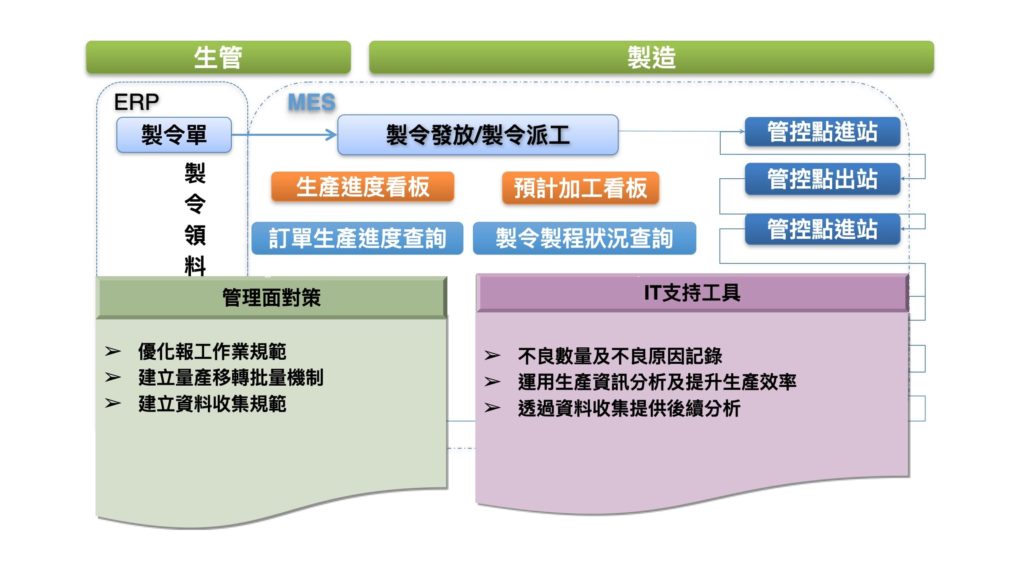
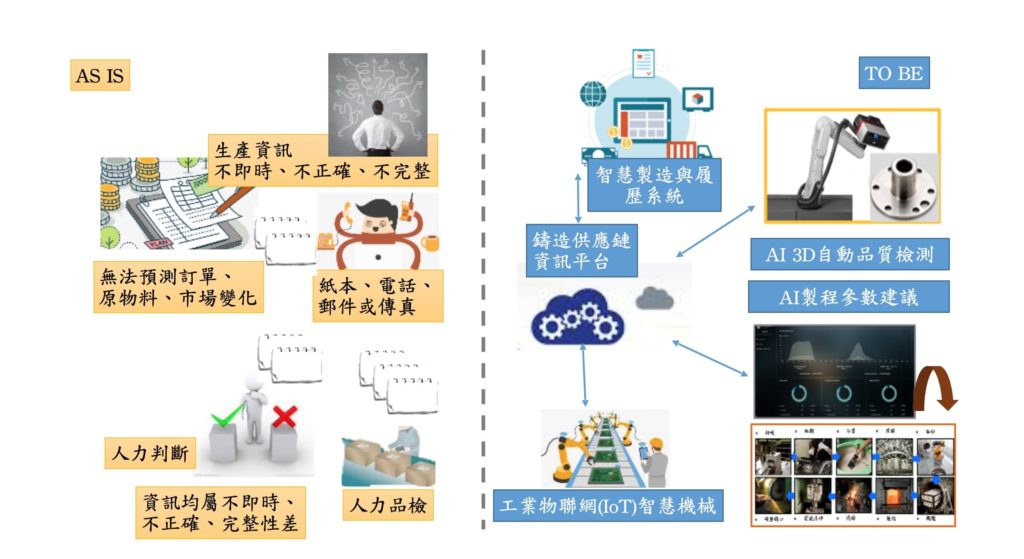
แผนผลประโยชน์ที่ได้รับ
อัตราผลตอบแทนจากการลงทุน (ROI)
อัตราผลตอบแทนจากการลงทุน (ROI): สามารถปรับปรุงความแม่นยำในการวางแผนการจัดเตรียมวัสดุ ลดปริมาณการจัดเก็บวัสดุคงคลังลง 15%;ปรับปรุงประสิทธิภาพกระบวนการผลิต ประหยัดกำลังคน เนื่องจากอัตราผลผลิตเพิ่มขึ้น ประหยัดกำลังคนในการซ่อมแซมและเจียระไน คาดการณ์ 18%
ประสิทธิภาพอุปกรณ์โดยรวม (OEE)
ประสิทธิภาพอุปกรณ์โดยรวม (OEE): สามารถลดอัตราของเสีย ทำให้อัตราการเกิดข้อบกพร่องลดลง 10% อัตราการใช้งานเพิ่มขึ้นเป็น 90% ประสิทธิภาพการผลิตยังคงอยู่ที่ 85% อัตราผลผลิตเพิ่มขึ้นเป็น 80% OEE เพิ่มขึ้น 9%
ลดระยะเวลารอคอย