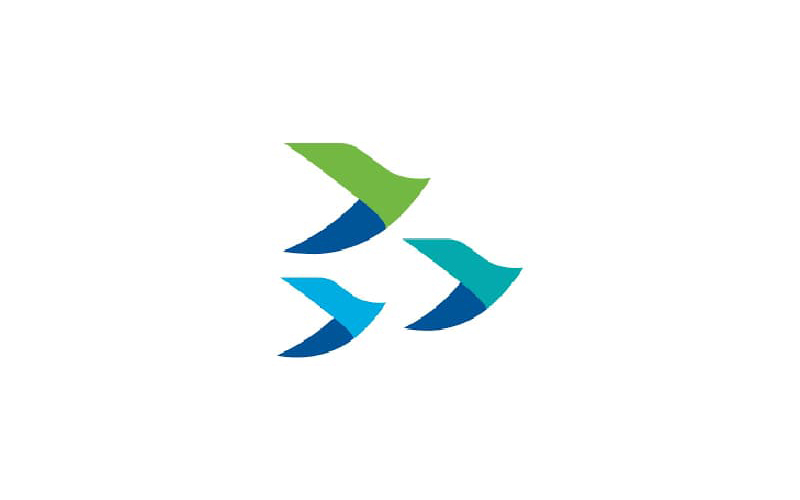
HY ELECTRONIC specializes in the R&D, manufacturing, and sales of diodes and bridge rectifiers. Entering mainland China in 1989, the company established Yangzhou Hongyang Electronics Co., Ltd. in 1992, now known as Yangzhou Hongyang Technology Development Co., Ltd. Its complete, advanced, and automated production lines are moving towards full automation. Annual production of diodes and bridge rectifiers exceeds 2 billion units, growing at over 20% annually.
The company’s product R&D focuses on CELL and GPP types. Packaging is evolving from single SIP/DIP to smaller SMD packages. HY ELECTRONIC’s products are widely used in computers, communications, automotive, and consumer electronics. The company is also actively developing new green energy products for applications in LED lighting, solar power, and automotive energy efficiency.
ManufacturingBottlenecks
1.Manual reporting and statistics for anomaly handling lead to delayed and non-transparent information flow.
2.Actual working hours of workstation personnel cannot be accurately estimated.
3.Real-time reporting and production status cannot be quickly grasped.
DigiHua IntelligentSolution Implementation
Unified Process Card Format
Challenge
Previously, run cards varied across plants, leading to format complexity, multiple templates for the same products, human error, and manual entry.
Countermeasures
Unified Process Cards: Improving Efficiency and Accuracy with Barcodes
Consolidation of R&D and Production Information
Challenge
Delayed communication of inspection specs between R&D and production prevents real-time access for production lines, causing discrepancies and potential errors between production and R&D.
Countermeasures
HY ELECTRONIC Why Informatization?
Give your boss first-hand information
Why Group Integration?
Put the information together and get what you need
Why do we need to trace the quality of automobiles?
Improve quality to satisfy customers
What do the units want?
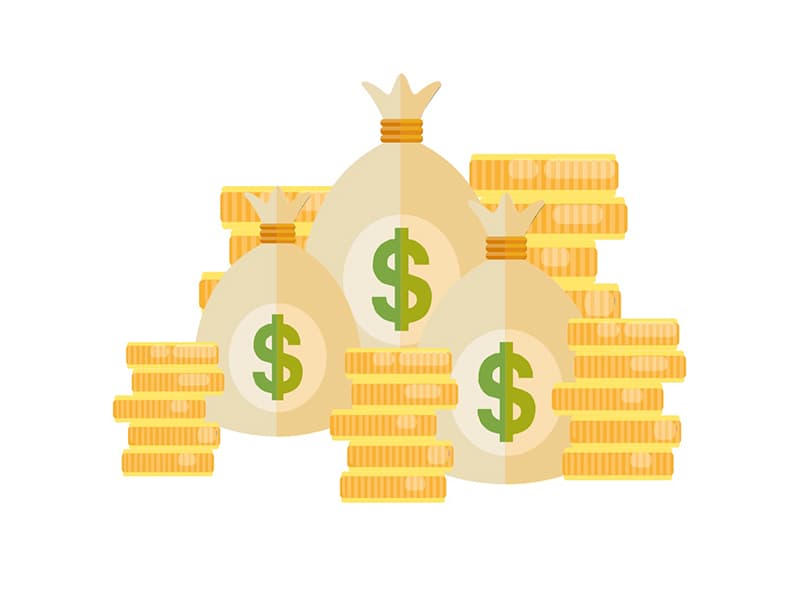
finance
We can now see the time spent at each station and compare actual working hours for processes and workstations.
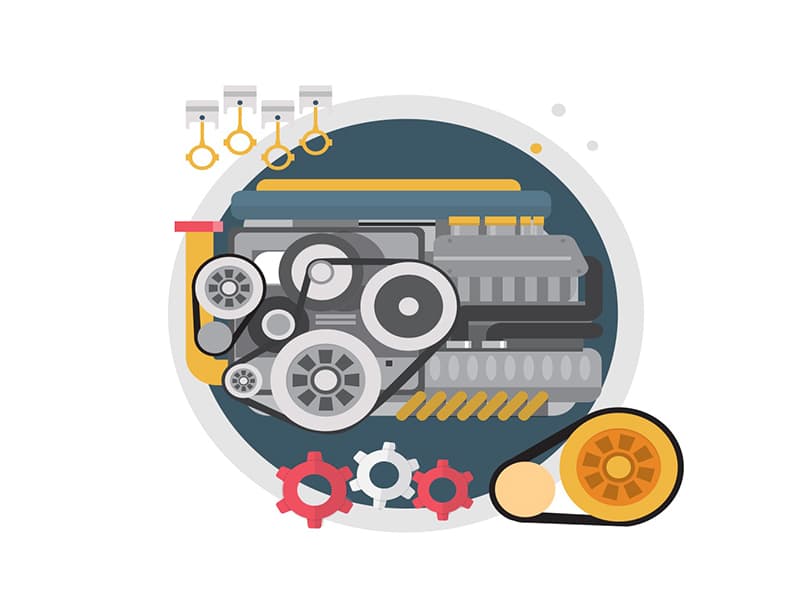
Production Management
Previously, production control relied on physically checking shop floor work orders. Now, they can access the system directly. Sales inquiries about production progress can now be answered directly using the system.
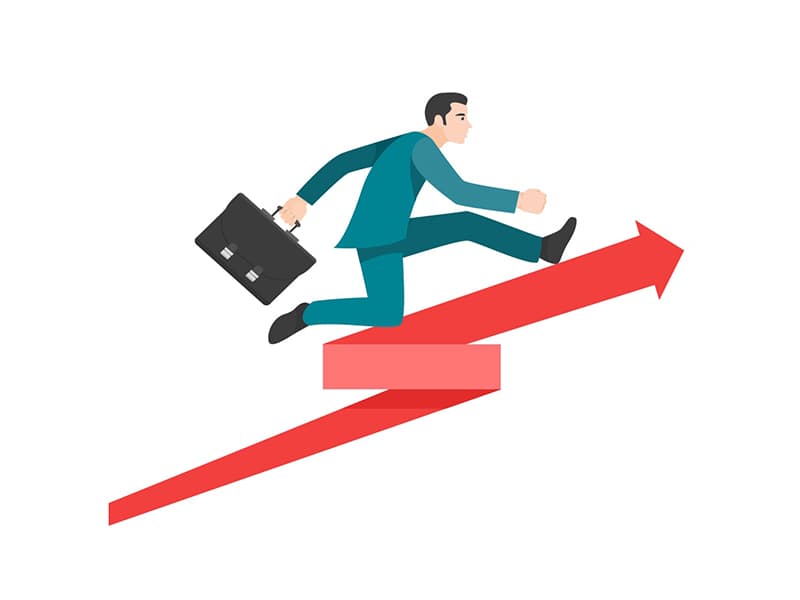
business
Production progress data enables order analysis to ensure on-time customer delivery or provide early warning of potential delays.