sMES intelligent shop floor
execution system
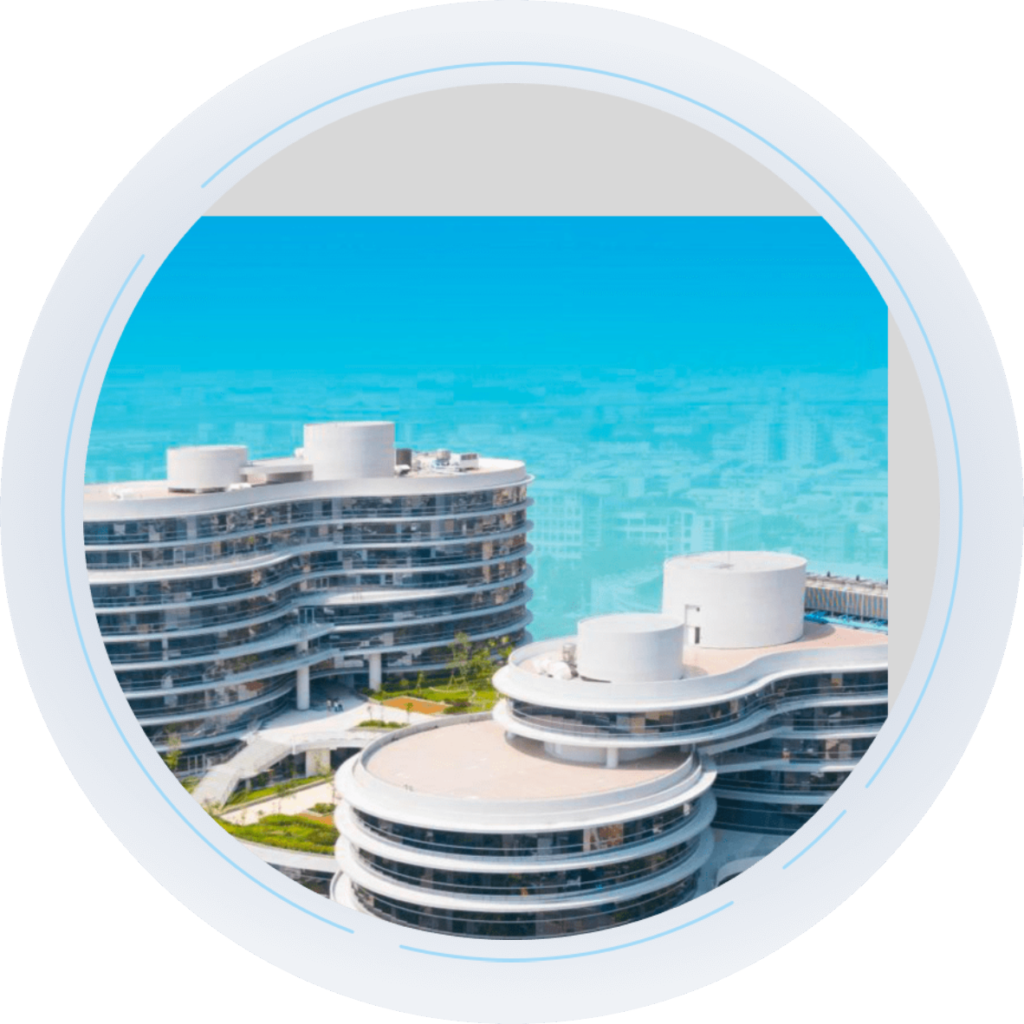
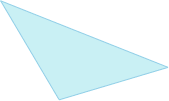
Smart Manufacturing Execution System
Time management is the competitive edge and lean production is the goal to build an intelligent factory.
Based on production tasks, breaking down the barriers between production management and execution, and constructing a closed-loop of data for the entire value chain.
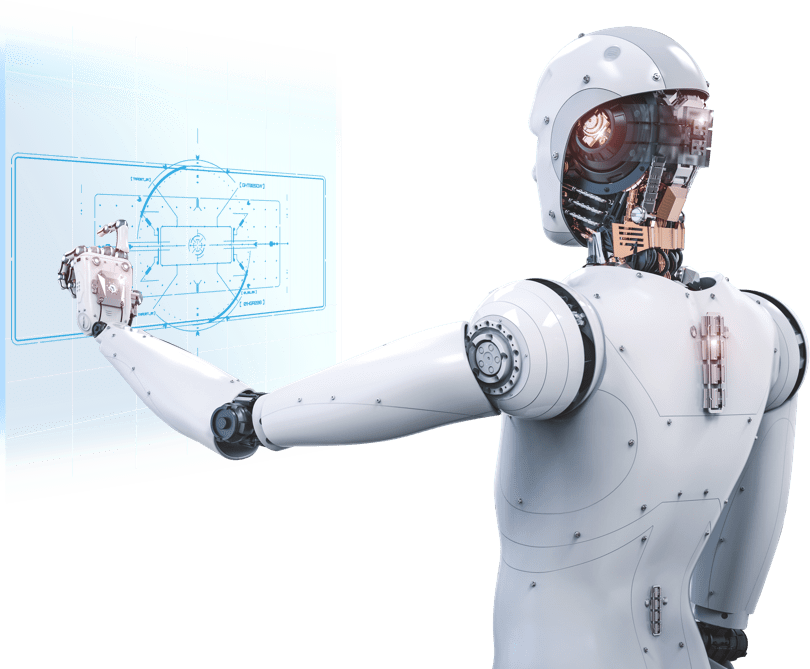
Focusing on man, machines, materials, methods, and measurements
Comprehensively analyze the pain points of production workshop management
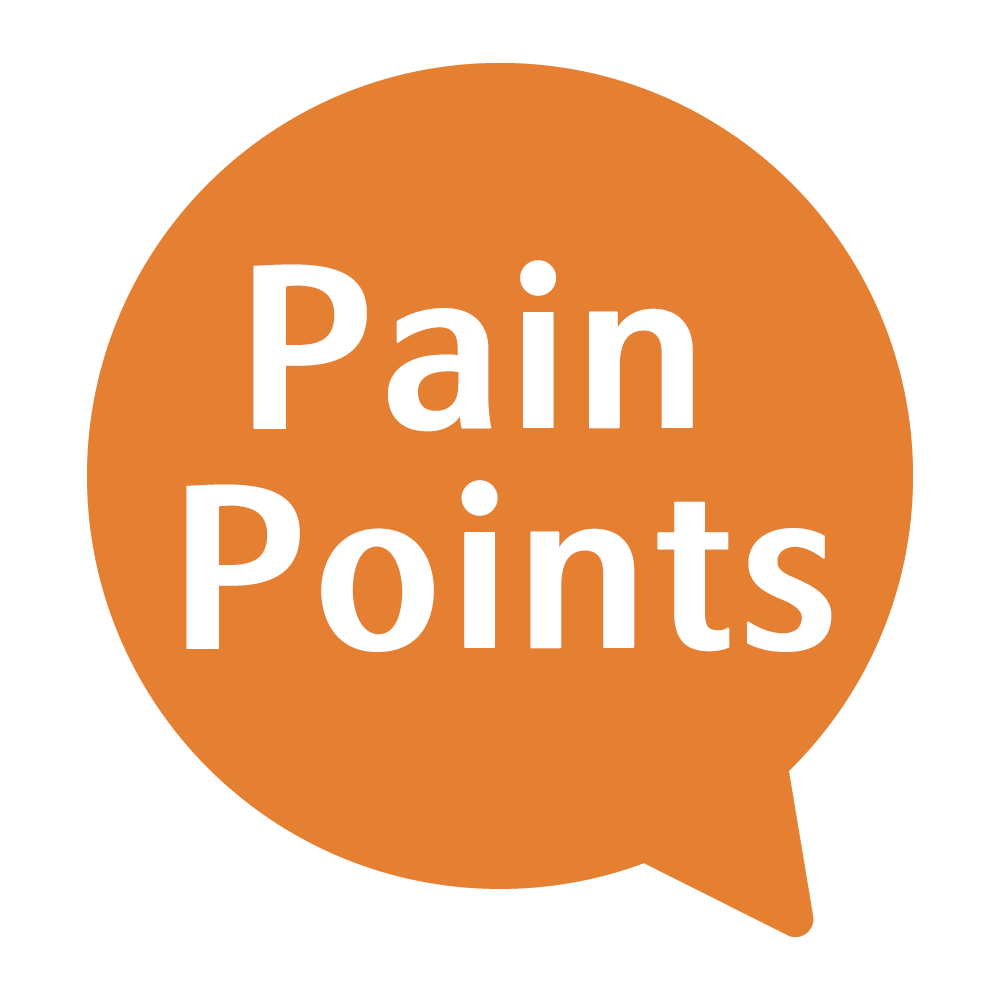
- Low equipment utilization rate:
Personnel who lack basic skills in operating equipment may cause equipment failures, damage to workpieces, etc., resulting in a decrease in equipment utilization rate and increased operating costs.
- Low yield rate:
Insufficient skills of operators may lead to low product quality and yield rate.
- Lack of knowledge accumulation:
Unable to convert personnel’s working hours into experience data to obtain objective data and establish an internal education and training mechanism within the company.
- Disorder in human resources:
Production line supervisors cannot clearly determine whether the operators have the ability to operate the equipment, resulting in incorrect dispatch and scheduling of human resources, and waste of human resources.
• Lack of standardization:
The lack of standardized maintenance plans for equipment results in inconsistent maintenance methods and frequencies, increases the probability of equipment failure, and reduces availability and production efficiency.
• Spare parts records are confusing:
There is no record control of maintenance spare parts.
• Paper historical information is confusing:
When checking historical data, looking through paper, the files are confusing and it is difficult to quickly check the maintenance plans and records of the equipment.
• No analysis report:
It is impossible to estimate maintenance efficiency and provide instant feedback on maintenance status archiving.
• No maintenance schedule:
It is impossible to arrange equipment maintenance programs in real time according to the production quantity and time.
• Wrong ingredients:
Using wrong parts and materials leads to a decrease in quality and yield, wastes time troubleshooting abnormalities, and increases operation and time costs.
• Frequent shutdown for materials:
Materials cannot be supplied immediately, and the demand for materials is interrupted, resulting in untimely supply and affecting overall production efficiency.
• Materials and accounts are inconsistent:
Failure to timely report work and debit accounts leads to inconsistencies in accounting materials, affects the efficiency of procurement and production management in judging production status, and increases heavy work.
The production process has high temporary variability. Temporary changes in processing technology or equipment during processing require high production flexibility. Abnormal processing often leads to supplementary orders or missing information.
• Paper records:
Inspection data and measurement records are recorded in paper, which is inefficient in searching and is easy to modify, making it unreliable.
• Different standards:
Check the inspection standards and use traditional instruments to measure. The inspection standards vary from person to person and cannot be unified.
• Abnormal warning is not real-time:
Only after sorting out the data can we know whether there are any abnormalities. If there are any abnormalities, please contact us by phone or send us an email yourself.
• Statistics are not easy:
Manually compile data and generate relevant reports. It is not easy to query and compile reports.
• Check for opacity:
Test results are not immediately known.
The core function of sMES
Achieve interconnectedness and intercommunication among man, machine, material, method, and measurement (5M), enabling efficient and effective production management.
• People management:
Includes various roles or positions in the production site, such as factory managers, production managers, dispatching supervisors, equipment operators, process quality control personnel, and equipment or mold maintenance personnel.
• Equipment management:
Includes the capacity of the equipment, equipment checklists, equipment maintenance, equipment utilization analysis, failures, repairs, and mold and fixture life and failure management.
• Material management:
Includes the basic properties, production process, and quality risk warning standards of finished products, semi-finished products, and critical materials.
• Method management:
Refers to the production methods, including equipment dispatch management methods, station in and out management methods, product process management, rework management, batch and sub-batch management, unit quantity conversion between processes or stations, and product component serial number rules.
• Measurement management:
Includes the input and warning management of in-house QC data, which can be seamlessly integrated into the Dinghua intelligent quality solution sQMS for more detailed inspection data chart analysis and the tracking and prevention mechanism of potential quality abnormalities.
sMES has four distinctive features that help enterprises build a digital factory
Feature 1.
Integration of Production and Enterprise Operations
Integration of Production and Enterprise Operations
Digiwin’s various ERPs are integrated through standard scenarios, and can successfully integrate with Digiwin’s various ERPs, Oracle, SAP,Yonyou Software, and Kingdee. Corresponding to different ERPs, only the corresponding interface needs to be replaced for instant switching, and information will not be lost. The integrated content includes work orders, production reporting data, work order materials, outsourced returns, and inventory. This allows the data of the enterprise’s production and manufacturing system to be reconciled with the data of the operation system, making the costs, progress, and history of related products more transparent, and the inventory quantity more accurate. This facilitates the management to analyze the internal operation status of the enterprise from different perspectives, thus expanding profits and maintaining advantages.
Feature 2.
Flexible Configuration of Process Flow
Through more intuitive and flexible process configuration, it realizes flexible production in various plants, and can support the rapid replacement or addition of processes during different product manufacturing or production processes. It achieves a low-code and easy-to-configure production execution system.
Feature 3.
Integration of IT and OT
Achieve modern industrial network architecture
In response to the trend of the Internet of Things, a unified entry point for integrating IT and OT data is provided. By using cross-domain technology, IT and OT data are integrated and configured to achieve not only the conversion, cleaning, and traceability of OT data but also the application of scenarios after the integration of IT and OT data
Feature 4.
Fully creating a visualized, transparent, and traceable production workshop
MES meets critical needs of enterprises such as product management, quality control, equipment integration and management, problem tracing and analysis, and real-time data collection in the production workshop. It provides a complete plan to achieve an intelligent workshop, and enterprises can integrate information technology requirements in stages according to industry characteristics, management methods or production modes, and other differences.
sMES Success case
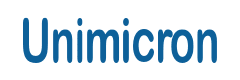
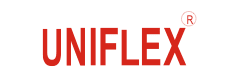
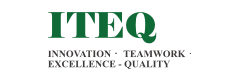
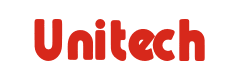
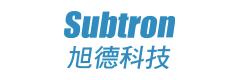